F&O is integral to U-M’s world-class research enterprise. Here are two examples of F&O teams adapting their work to support researchers in the COVID environment.
Virtual biosafety lab inspections
Can a lab inspection be done virtually? In some cases, yes!
When research started ramping back up, the Environment, Health and Safety Biosafety Team sought a way to complete annual inspections of labs that work with biological hazards (such as bacteria, viruses, fungi, or blood) while respecting the need for reduced density.
Fortunately, biosafety inspections lend themselves well to virtual methods since they focus heavily on talking to researchers about how they handle biological materials.
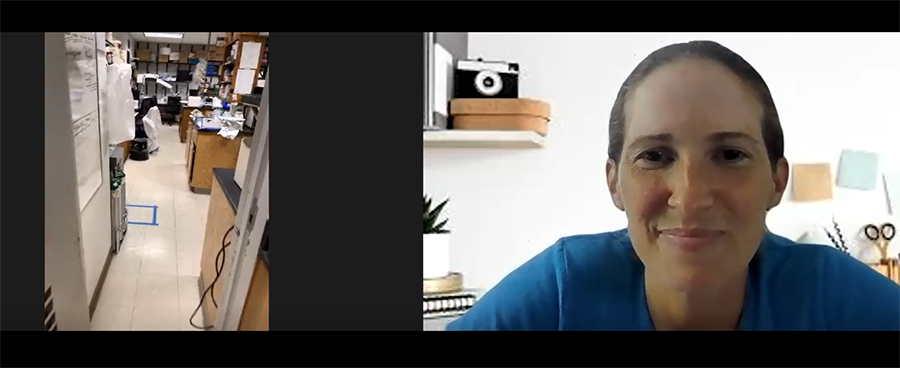
The Biosafety Team categorized their standard inspection questions by whether they could be assessed remotely. They determined that the majority of the questions worked remotely, and even items they’d normally look at could be seen on video instead of in person. For instance, one of the items is to check that equipment is certified. “I’ve had people take me around the lab on their cell phone,” says Crystal O’Donnell, a member of the Biosafety Team. “They can show me the sticker from EHS to verify it’s certified.”
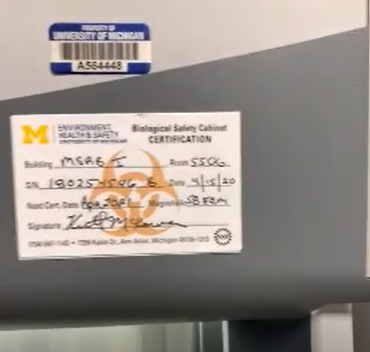
A virtual inspection hinges on a trusting relationship. Crystal notes that “After so many years working with the same people, we have a strong relationship.” Still, per their new guidelines, some biosafety labs aren’t eligible for a virtual inspection. Biosafety labs doing COVID research, run by a first-time U-M researcher, or any lab with compliance issues in the past must still have an in-person inspection.
Virtual inspections have pros and cons. Scheduling is easier, of course, and Crystal has found that screenshare has made it easier for researchers to quickly pull up their records or for her to walk them through something on her end. Cons include occasional connectivity issues and not being able to see everything in the lab that might prompt a question or recommendation.
Overall, Crystal says, the Biosafety Team and researchers are working together to “make the best of the situation we have right now. We’re adapting, like everyone else. We want to get back involved the way we were before, it’s just a new way to do it.”
Reconfiguring the ChEM Reuse Program
The ChEM Reuse Program, operated by the Office of Campus Sustainability for nearly 10 years, supports U-M labs and U-M’s waste reduction goal by enabling surplus chemicals, lab equipment, and materials to be used in other campus labs rather than being sent out for disposal.
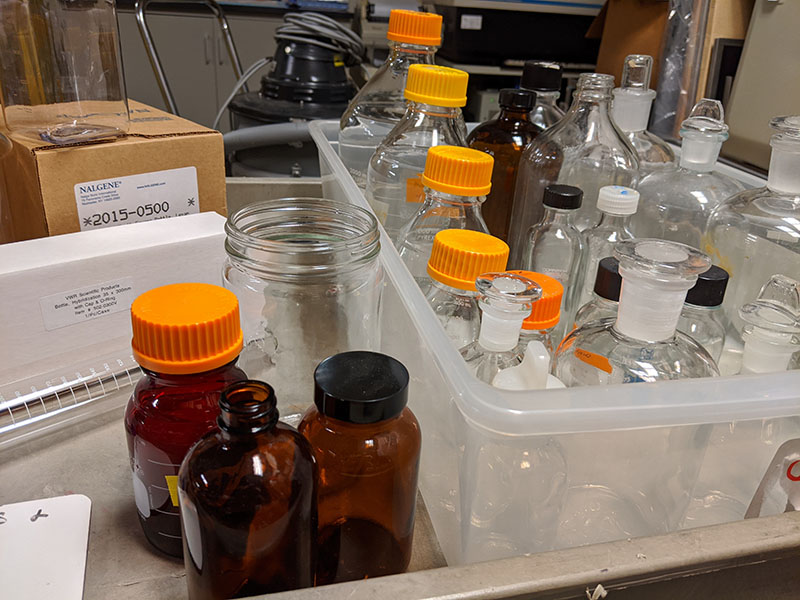
Like so much of the university, the ChEM Reuse Program paused operations in March. However, once research operations started opening up, there was a clear desire among researchers to use the program.
Several adjustments were needed to restart safely:
- In-person appointments, which accounted for 50% of last year’s program activity, could not be conducted in a safe, socially distant manner. Therefore, all orders are placed by browsing the inventory online.
- Deliveries, once made directly to the lab, are now being conducted at loading docks whenever feasible.
- The program staff condense all on-campus activity to one day per week to minimize on-campus presence.
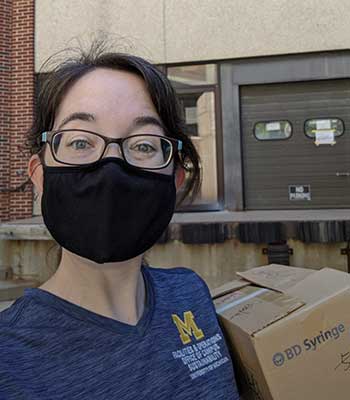
Our research community has embraced these changes in the name of safety, and have found value in waste prevention and money-saving aspects of the program. Users of the program include newly established labs or post-docs looking to stock basic supplies, labs looking to acquire supplies on back-order from usual suppliers, and labs aiming to be fiscally responsible or sustainable in their operations. Since resuming operations in July, the program has rehomed over 500 pounds of supplies valued at over $11,000 if they had been purchased new.
With demand for the program higher than ever and a track record of adjusting operations for efficiency and safety, ChEM Reuse has proven to be an enduring success.